The replacement of the old modalities for mobile maintenance by
A future-proof, intuitive concept – using the latest technology
the existing hardware. The NEO Mobile Suite and a dedicated team can do it! With new flexibility and transparency in maintenance. And with seamless integration of the customer’s proven upstream and downstream processes.
Customer benefits
Customer
WAGO GmbH & Co KG
Branch
Automation and electrical engineering
Contact
Stefan Westermayr
Team Leader SAP Customer Service and Asset Management
+49 89 456785839
Contact us
An original patent stands at the beginning of WAGO’s history: spring clamp technology. On this basis, WAGO Klemmenwerk GmbH is founded in Minden in 1951. Since then, a whole host of other “patented solutions” have been added. Today, the WAGO Group is one of the leading international suppliers of connection and automation technology. With products that are used worldwide in energy, process and building technology as well as in mechanical and plant engineering and transportation technology.
The WAGO Group includes nine international production and sales locations, 19 other sales companies and the software specialist M&M Software. WAGO’s credo for both its customers and its approximately 9,000 employees in over 80 countries is: reliable, solution-oriented, partnership-based. A claim that also
defined the requirements for the new mobile maintenance solution.
From SAP Work Manager to intuitively flexible maintenance management
2017 saw the introduction of SAP in maintenance at WAGO, combined with the introduction of the first mobile maintenance tool, SAP Work Manager, for maintenance tasks. This has already led to a noticeable reduction in workload. However, the discontinuation and the associated cessation of further development meant that the desire for a successor solution grew relatively quickly.
In addition, there were further criteria from WAGO. Mobile document management was a key requirement so that maintenance teams and fitters can access all relevant data and information on the move. Also very important here: the transfer of attachments, because a picture on site often says more than the famous 1,000 words. In addition, comprehensive language packages in the system, as the solution is being rolled out internationally. And in terms of user-friendliness, the established and learned processes should be retained as far as possible. The same applied to the hardware.
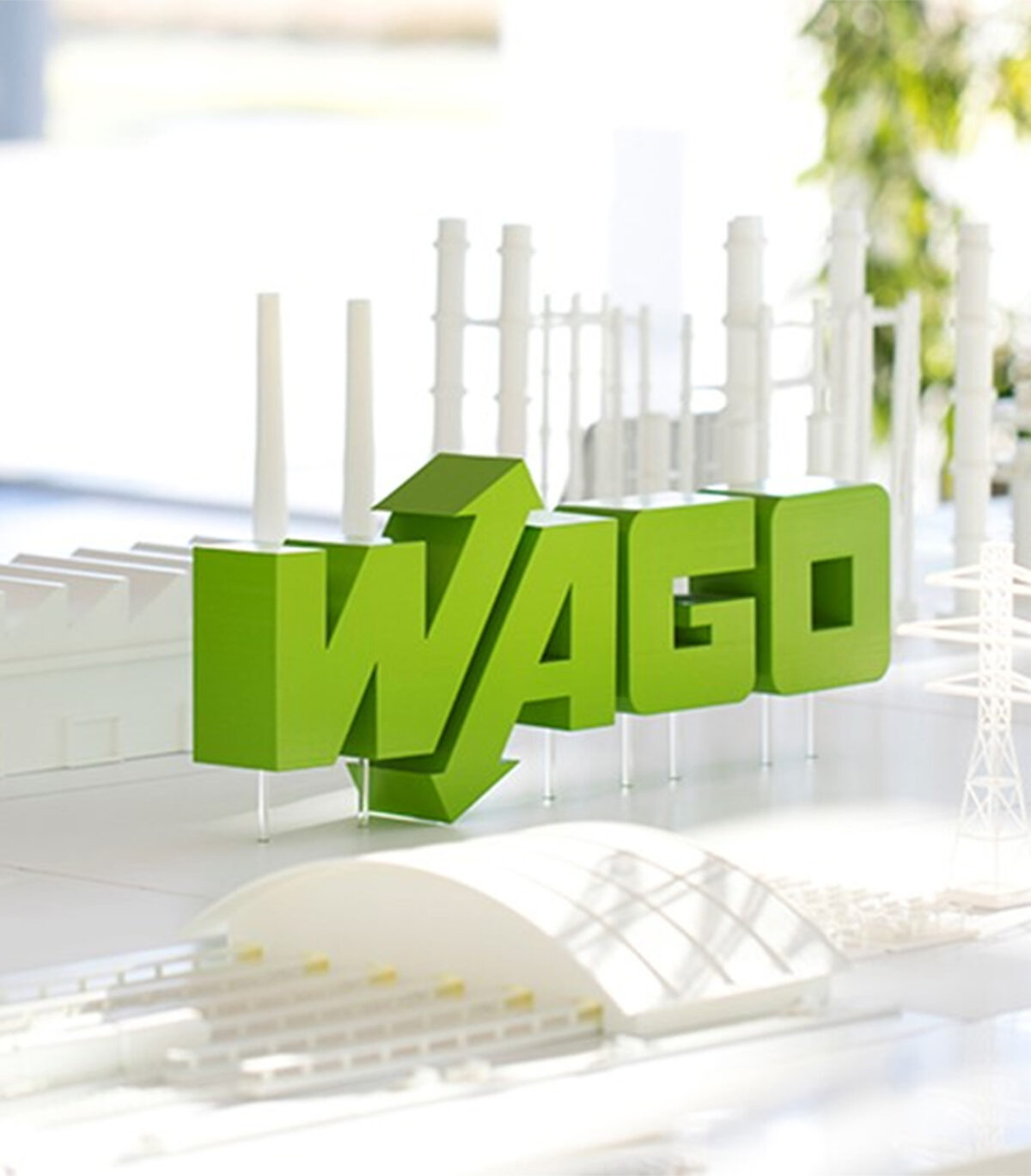
Maintenance in all aspects: from checklists to ad hoc orders
With the NEO Mobile Suite, all user groups in WAGO’s maintenance process received a tool optimized and configured to their individual requirements. For example, checklist editing with a clear display of all items to be processed and a significantly expanded range of functions. Or the identification of automatic follow-up measures in the event of non-compliance. All with generally intuitive handling.
Additional features are required for pool orders. These are tasks that cannot be handled by one person alone – so all information and all relevant parameters must also be available to several employees reliably and simultaneously. In addition, the data is recorded centrally in a maintenance order instead of in individual logs.
Not to forget: immediate repairs. For example, at short notice on the way to or from an order – or as troubleshooting that has to be carried out ad hoc. Here too, the NEO Mobile Suite ensures rapid recording and coordination plus a reliable database. Without any lengthy administration or distribution. Everything is documented on a screen in the display: Entry of the notification, creation of the order as well as confirmation and completion in one step – without having to initiate data synchronization in between.
Simply uncomplicated: from Go Live to Go Work
A key point in the go-live process was WAGO’s desire to convert the existing maintenance instructions from the SAP standard to the new mode. This also included rescheduling the corresponding maintenance plans. 1,000 in number. Including new assignment of processes. This complex task was implemented together with the Axians team.
From the definition of requirements to testing and fine-tuning, not only WAGO’s IT specialists were involved, but a complete team from the user to the IT department. A particular focus was placed on the electricians, assembly teams and other professionals in the maintenance service. For “wind and weatherproof” usability under operating conditions.
Another extra of the NEO solution: more flexibility for every user with the devices. Although everyone had previously been using iPads, WAGO also wanted the option of switching to Android or working on Windows. No problem with the NEO Mobile Suite.
In addition to the greater flexibility and performance of the new solution, the processes mentioned are now also more configurable than before via mobile customizing.
And on it goes: from the sensor to the cloud - and back again
With the implementation of the NEO Mobile Suite, WAGO has also laid the foundation for further innovations in mobile service. Holger Schlink, project manager at the customer, formulates his vision as follows: “The system reports independently at the right time with a maintenance order and indicates the components that need to be replaced or repaired. At the same time, the system also ensures that all the necessary resources are available at the right time.” IoT (Internet of Things) sensor technology in conjunction with analytical AI and the cloud is already being considered at WAGO.
Axians and the possibilities of the NEO Mobile Suite are also part of this step. With creativity and expertise for the best connections.
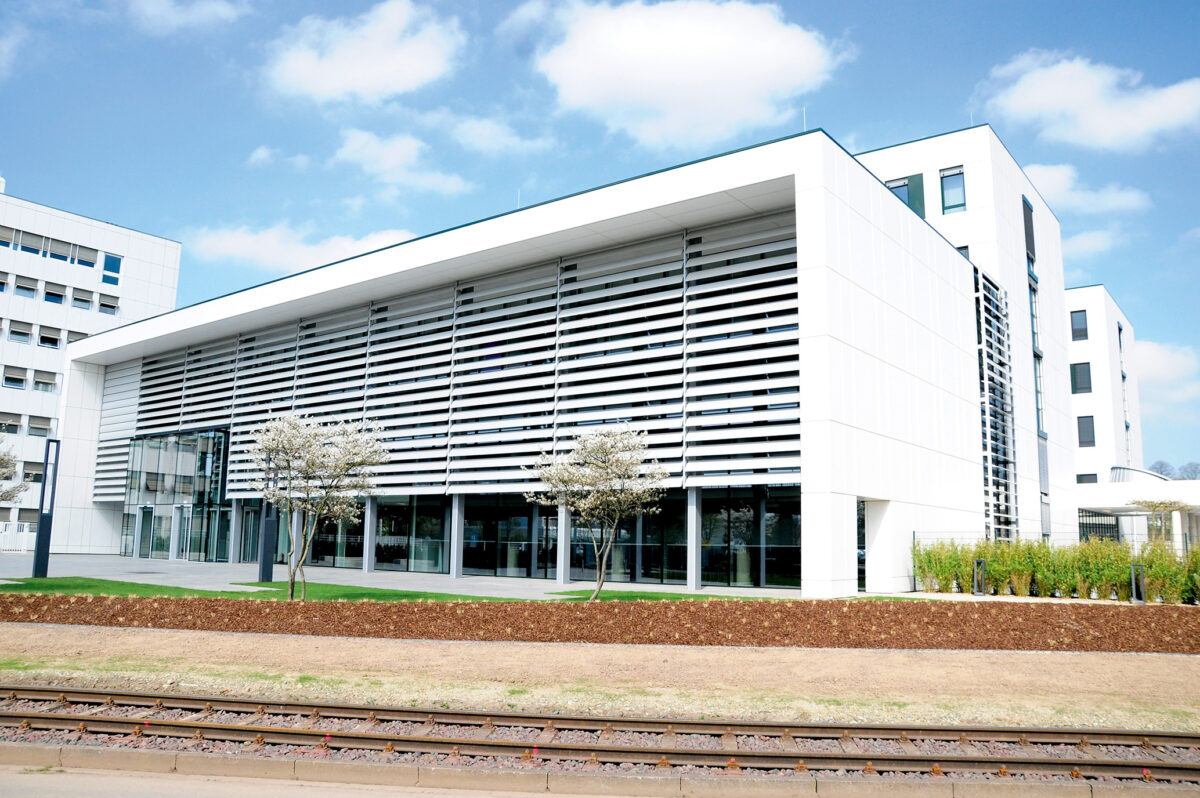
![[removal .ai]_57bd8b81-5168-4d9c-a1cf-dc893e596123-holger-schlink Portrait von Holger Schlink](https://www.neo-suite.de/wp/wp-content/uploads/2023/12/removal.ai_57bd8b81-5168-4d9c-a1cf-dc893e596123-holger-schlink.png)
Never touch a running system? Of course! That works. Together as a team. And with a project partner who is committed to the common cause with expertise. After evaluating six providers, including a proof of concept, we finally opted for the NEO Mobile Suite from Axians. A good choice for our requirements for the new mobile maintenance solution. From functionality and flexibility to service and support. For all new features, one criterion was particularly important to us: the established and learned processes at WAGO should be retained as far as possible. The new system should therefore adapt to us - not the other way around. In this sense too: mission accomplished.
Vice President Real Estate International, WAGO GmbH & Co. KG
WAGO strengthens connections. Worldwide. And also when it comes to service.
The WAGO Group is one of the leading international suppliers of connection and automation technology and interface electronics. The family-run company is the world market leader in the field of spring clamping technology. WAGO products and solutions ensure safety and efficiency in industry, in railroad and energy technology, in the marine and offshore sectors and in building and lighting technology.
Since its foundation in 1951, WAGO has grown steadily and today employs around 9,000 people worldwide, including around 4,200 in Germany at its headquarters in Minden in East Westphalia and Sondershausen in Thuringia. In 2022, turnover amounted to 1.34 billion euros.
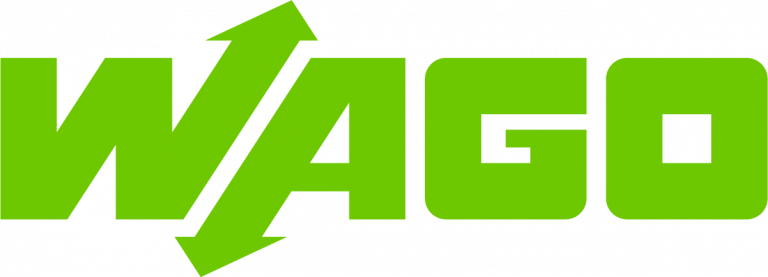