Today, we can collect and evaluate machine data on an unlimited scale. Anomalies that can be read off from this form the basis for predictive maintenance. With NEO Predict – our predictive maintenance module for maintenance and field service processes – you can reduce your maintenance costs and extend the service life of your machines. As a service provider, you offer your customers unique service quality with the help of NEO Predict.
Predictive Maintenance - Prevent failures with NEO Predict
Advantages of Predictive Maintenance at a glance
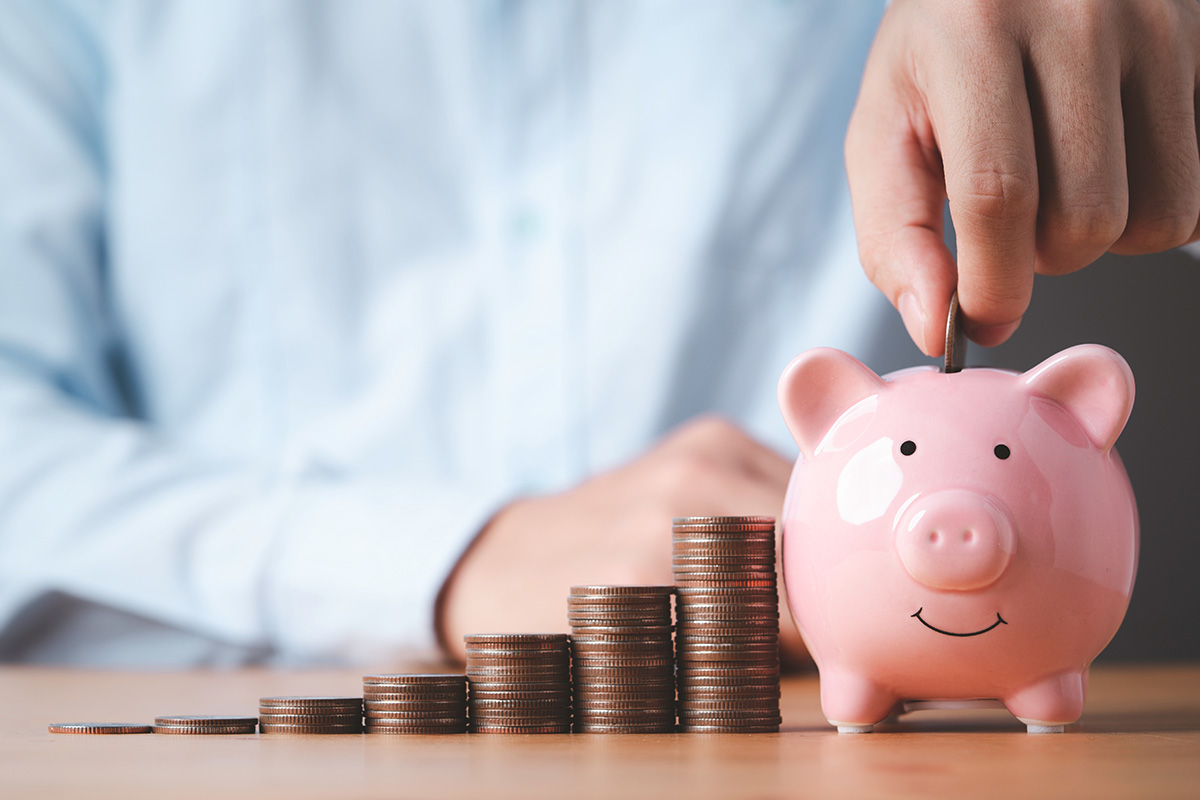
Cost reductions
Through the predictive maintenance of plants, companies can minimize acute fault messages in their own maintenance or also in the service offering for their customers. This significantly reduces the total cost of ownership.
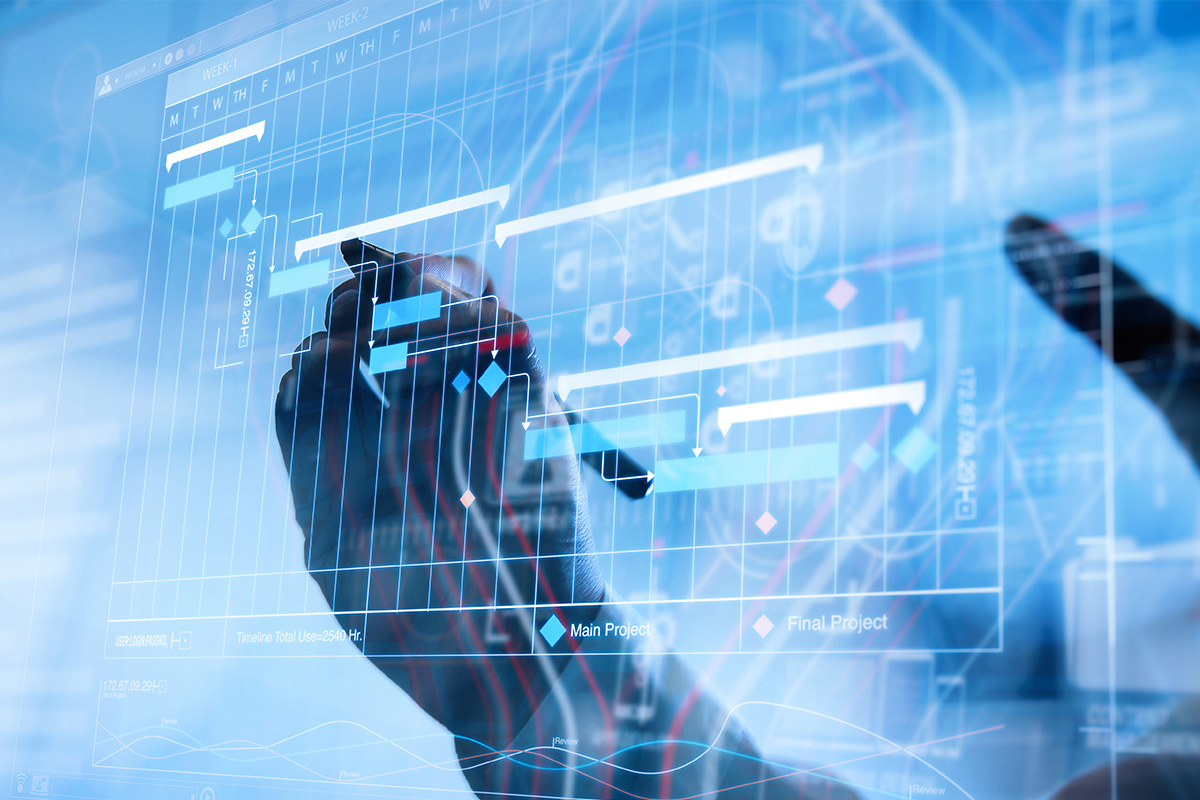
Higher plant availability
With predictive maintenance unplanned downtimes in production are avoided through real-time monitoring and malfunctions can be responded to automatically.
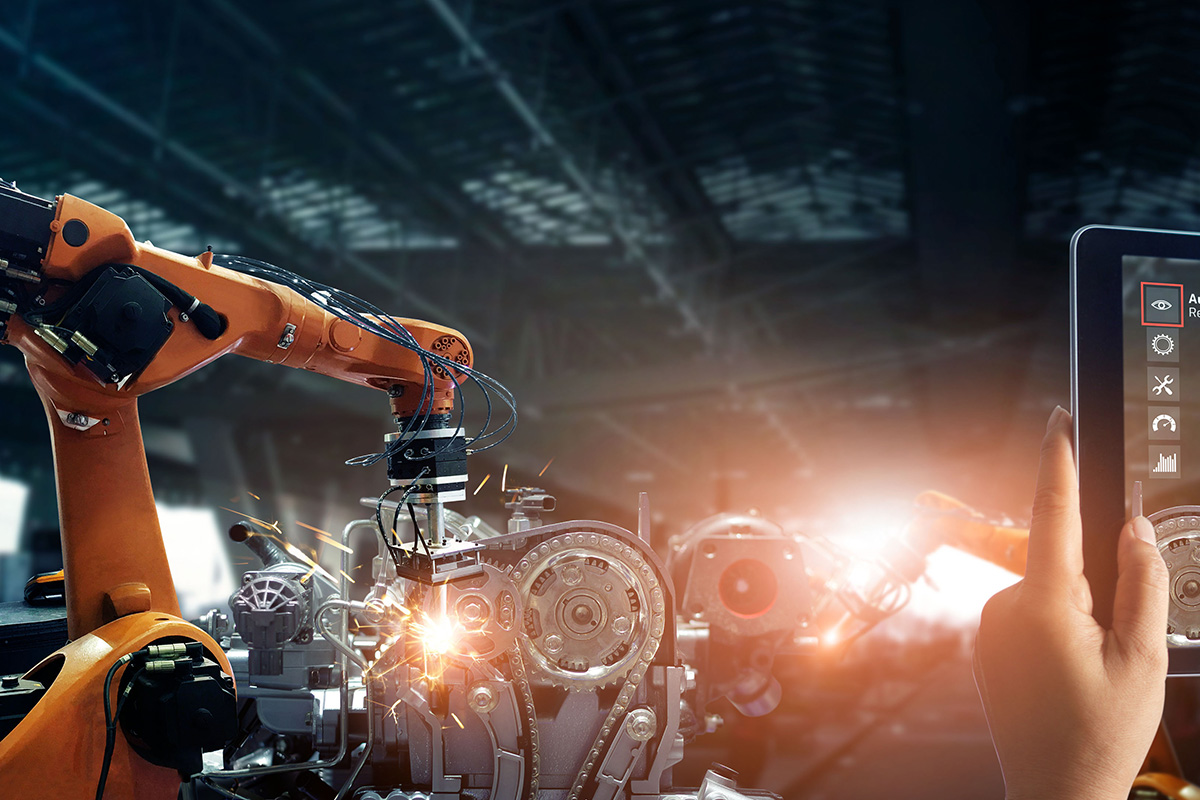
Extension of the machine service life
Continuous monitoring and proactive maintenance of machinery and equipment leads to an extended service life.
Screenshots from NEO Predict
Main features of Predictive Maintenance
Technical specifications
A data mapping links the machine with the equipment in SAP and associated measuring points.
The messages or orders created in NEO Predict run directly into the NEO Schedule scheduling module. Here, the maintenance order is planned and sent to the technician for further processing via the mobile solution NEO Mobile.
If required, automatic adjustments can also be made for maintenance plans in SAP to call maintenance calls earlier, or to extend the planned cycle.
NEO Suite references
Do you have any questions?
Contact our expert Gertrud Kleinert, NEO Suite Sales Expert.
Phone: +49 731 1551783
Mail: gertrud.kleinert@axians.de
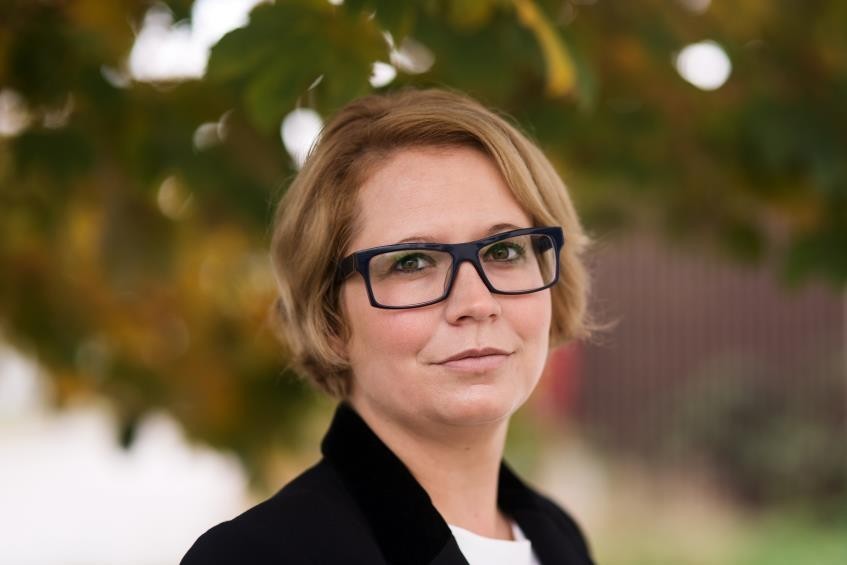
You are currently viewing a placeholder content from HubSpot. To access the actual content, click the button below. Please note that doing so will share data with third-party providers.
More Information