Maintenance software offers various potential benefits. These relate to planning processes, the execution of maintenance activities or downstream processes. These include:
Maintenance software components
Maintenance software consists of a job planning or scheduling tool like NEO Schedule and a mobile solution or app like NEO Mobile for maintenance workers.
The maintenance planners use the scheduling software to plan the orders for the maintenance staff.
The maintenance staff receive their orders on their smartphone, tablet or laptop via the mobile solution or app. This contains all the necessary information about the order. After they have completed the maintenance or repair, they document their work in the app. This data is then transferred to the back end, where it may be checked, further processed and archived.
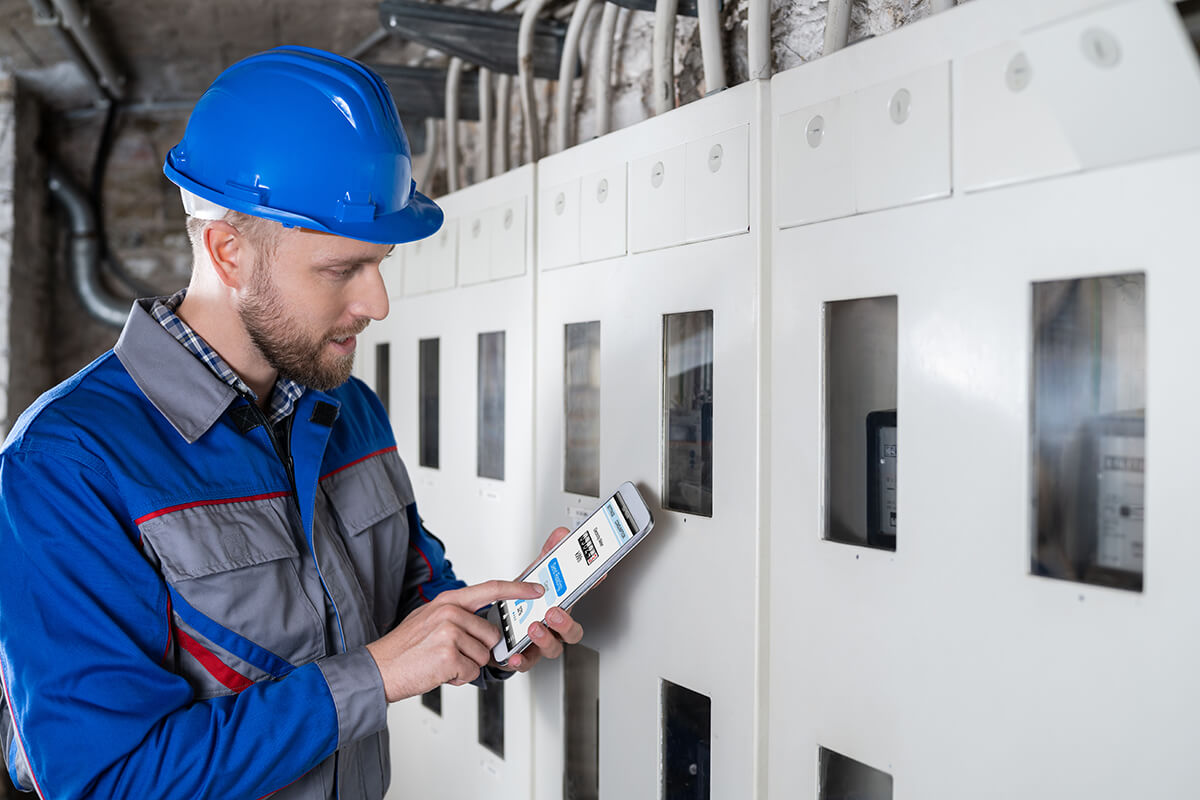
In addition to the two main components of the deployment planning and mobile solution, there are other modules that complement the maintenance process and can map it digitally from end to end.
These include, for example, augmented reality applications and modules we NEO Remote Service and the AR Worker support maintenance staff on site with virtual instructions or experts from a distance.
Dashboard modules such as NEO Insight provide analyses of the data collected by the maintenance staff and thus enable maximum transparency of machine conditions, processes and productivity. This provides decision-makers with an optimal basis for their capacity and resource planning.
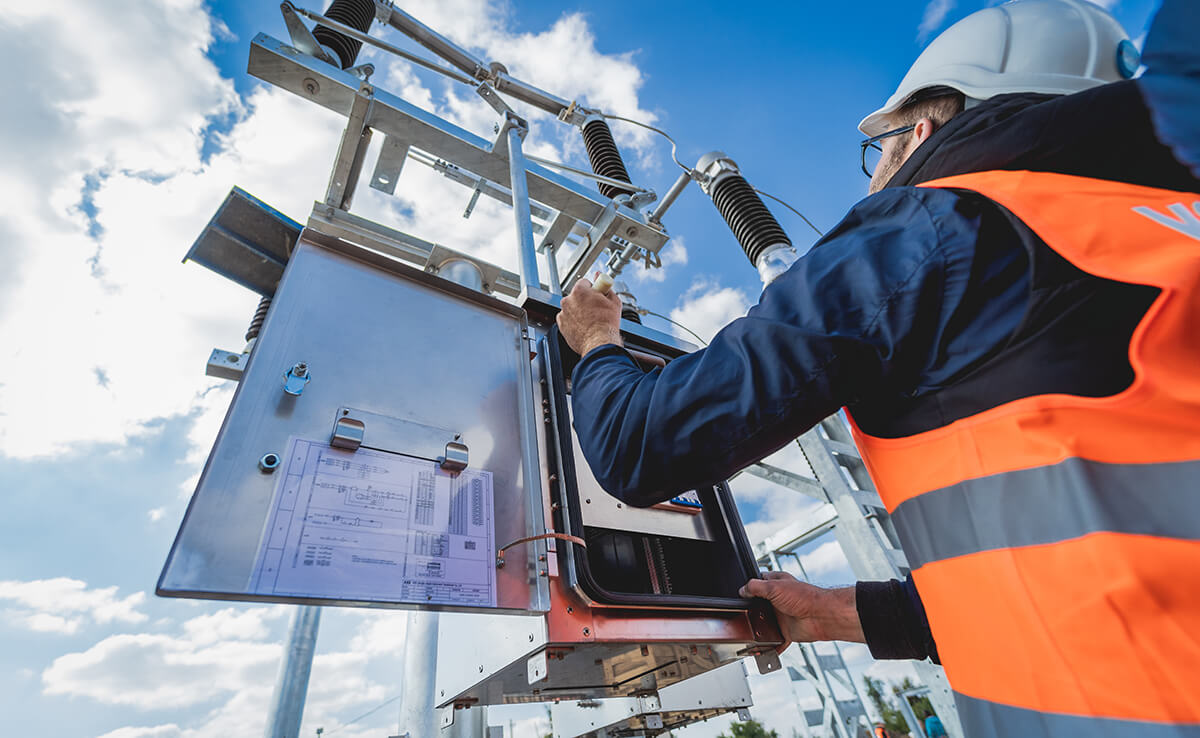
Advantages of maintenance software
Industries for maintenance software
The industries for which the use of maintenance software is relevant are as diverse as the potential benefits of maintenance software. What they have in common, however, is the presence of a high number of assets, as well as movable or non-movable assets. These include:
- Various manufacturing industries with a wide range of production equipment and machinery.
- The Energy Supply, this concerns both utilities with e.g. large power plants and public sector operations with regional generation and a regional distribution network.
- Telecommunications company with telecommunication networks, server and communication equipment.
- In the industry Health and pharmacy with medical equipment and production facilities for the manufacture of medical products.
- In the industry Transport & Logistics In the context of fleet maintenance such as trucks, aircraft or ships.
- The real estate industry through facility management with regard to heating, ventilation or even air conditioning systems.
- Mining company in the context of mining and transportation equipment.
- Various companies construction industry as part of their fleet or mobile construction equipment.
Main functions of maintenance software
The functional areas of maintenance software can be mapped modularly via individual applications or platform-integrated. The functional areas include maintenance planning, the execution of maintenance processes, and the documentation and evaluation of resulting results.
Company size for maintenance software
The use of maintenance software can be beneficial for companies of all sizes. The decisive factor is which type of software is to be used in which maintenance context. A scheduling tool may be necessary, for example, when the scheduling process becomes unmanageable or inefficient, or when AI-based scheduling is intended to optimize the utilization of maintenance workers. A mobile application makes e.g. makes sense in the case of spatially separated plants, if a maintenance technician has a travel route and can thus take the necessary information about the plant with him digitally instead of in paper form.