Plant maintenance with NEO Mobile means: standardization and digitization of objects and processes. In addition, full transparency of all work performed or to be performed and expenses. And also an immediate fulfillment of increased requirements for proof of measures.
Customer benefits
Customer
BELIMO Automation AG
Branch
Building services | Building automation
Contact
Stefan Westermayr
Team Leader SAP Customer Service and Asset Management
+49 89 456785839
Contact us
Maintenance without waiting. Established and individualized in SAP standard.
Energy efficiency in buildings – a “very hot” topic today. However, BELIMO Holding AG has been successful in this field for almost 50 years. Founded in 1975, the company is now the world market leader in the development, manufacture and sale of field devices for the energy-efficient regulation and control of heating, ventilation and air-conditioning systems. The company, which is listed on the Swiss stock exchange, has more than 2,200 employees worldwide and operates in over 50 countries.
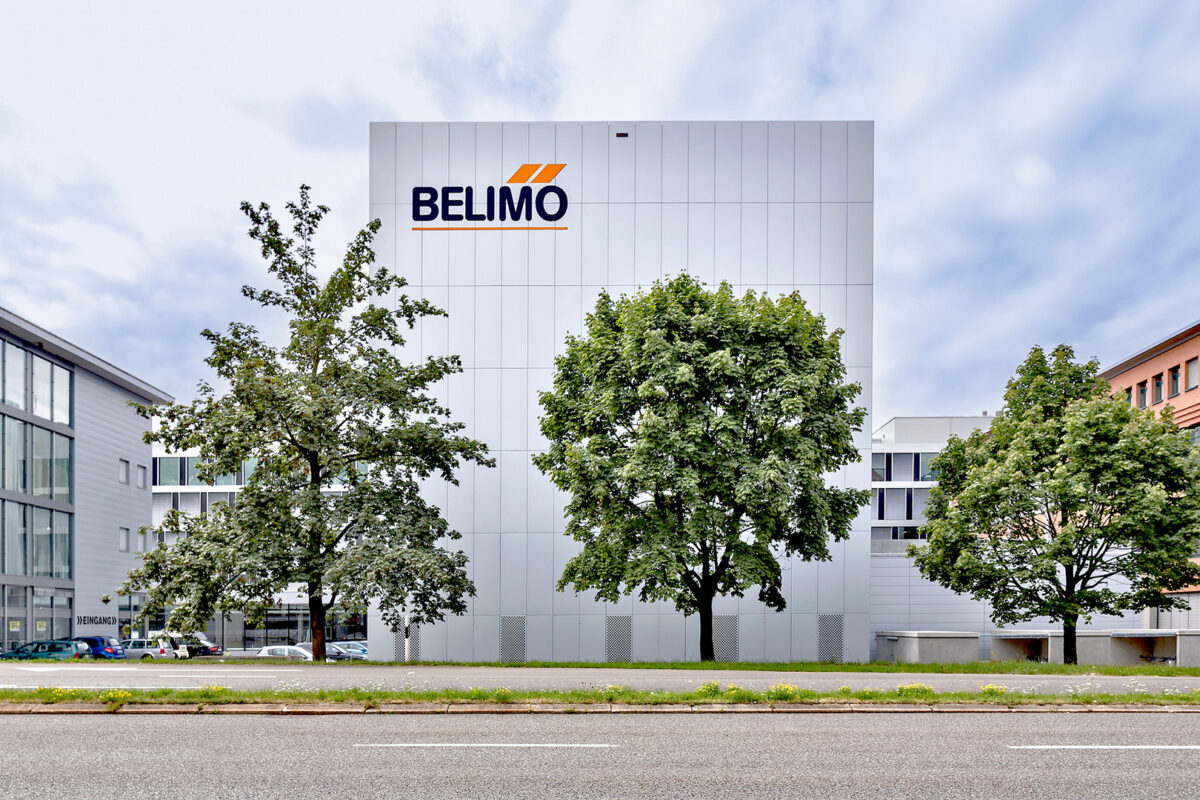
Strong growth requires strong structures.
A challenge for BELIMO, as for many other companies with strong growth: The core business is increasing enormously – the further development of the processes must keep pace. And that with more and more machines and significantly longer transport routes. Especially the topic of maintenance became a much stronger focus at BELIMO – and with it the offer of Axians NEO Solutions & Technology GmbH.
Prior to the start of the project, different processes were in place at the individual sites to identify objects and document necessary or implemented measures. These processes were usually matched to the plant or equipment and allowed it to operate efficiently there. However, it was difficult to merge the different processes for overarching planning and analysis. The lack of mobile usability and extended normative requirements ultimately tipped the scales in favor of looking for ways to standardize the database and processes and make them available on mobile devices as well.
With the introduction of processes based on SAP PM/EAM in conjunction with NEO Mobile Suite, these times are now a thing of the past. The result is an easy-to-use, standardized, mobile solution – specifically tailored to the requirements of maintenance technicians and for mobile scheduling. Thus, BELIMO also benefits from future SAP developments – simply in SAP standard, but still customized.
The rollout project was successfully completed in December 2021 and has since been rolled out to additional sites. As part of the project, approximately 9,000 pieces of equipment, 5,000 documents and more than 800 maintenance plans were recorded, and approximately 25,000 maintenance orders are processed on a mobile basis each year.
Team player, flexible and pleasantly uncomplicated.
Mobile maintenance places special demands – on the professionals on site and the tools of choice. BELIMO needed a small, individual solution for this. But with fast access to all necessary plant and order-relevant data – mobile as well as offline. In addition, with a flexible extension or change of the master data offered via NEO Mobile App. And it’s all easy to handle and intuitive to use.
Thanks to NEO Mobile, team leaders are now in a position to easily distribute upcoming orders to the executing crew – and dispatchers can easily reschedule. In the mobile solution, external services can also be included and external materials can be viewed.
Production at BELIMO also works with the mobile app: as initiators for fault messages, executors for simple, planned maintenance and final instance for the final acceptance of systems. A mode that also supports the shift in service from reactive to proactive.
Sizing at its Best. Customizing at Work.
The requirement was to introduce and set up maintenance processes based on SAP PM/EAM. These were established in accordance with SAP standards and specifically designed to meet BELIMO’s requirements. For this purpose, master data and maintenance plans were initially set up in the system.
A special feature of NEO Mobile in this project is the push technology – as a key factor for the notification of new maintenance tasks. Even if the application is not actively used.
Another extra is the “master app” with mobile scheduling. This is because the maintenance employees at BELIMO act in a kind of hermaphroditic role: both as maintainers and dispatchers. With this in mind, they now have the additional option of distributing pending tasks on the move – for flexible and faster completion of upcoming tasks.
And important for use in the “wild”: the hybrid use of offline and online data. Certain data that is essentially only required “online” can be decoupled from the “offline” data. For example, linked attachment documents can be downloaded only when needed, while new messages are kept offline to make them available in areas without WLAN.
Conclusion: mobile success factors in a nutshell.
- Company-wide harmonized maintenance processes
- Transparent and central control on site by BELIMO maintenance foremen
- No media discontinuities in documentation and in the recording of maintenance data
- The management of master data, order preparation and the complete recording of activities performed is carried out via the NEO Mobile Suite and can thus be accessed from anywhere at any time.
- Significant increase in employee productivity through intelligent control of pending tasks
- Pool scheduling (self-scheduling) for the most necessary freedom – and also for more productivity, as maintenance teams can complete already released jobs at nearby plants on their own initiative.
Compared to the competition, the NEO offering was able to deliver a coherent overall concept for us. The combination of consulting know-how for the introduction of best-practice processes in the SAP environment and the user experience offered by a mobile application was particularly convincing. In addition, there was a tightly timed process introduction with parallel working methods when establishing the new solution. All of these factors contributed to the high level of user acceptance in practical use.
Senior Project Manager for Production & SCM, BELIMO Switzerland
BELIMO. Well on the way in terms of building efficiency.
BELIMO stands internationally for competence with effective efficiency in the building sector. Founded in 1975, the company is now the world market leader in the manufacture and sale of field devices for the energy-saving regulation and control of heating, ventilation and air-conditioning systems – based on sensors, damper actuators, control valves and meters. Innovative strength is a key factor here. Here BELIMO works closely with its customers to develop new and sustainable solutions. Belimo has around 2,200 employees worldwide and has been listed on the Swiss Stock Exchange (SIX) since 1995.
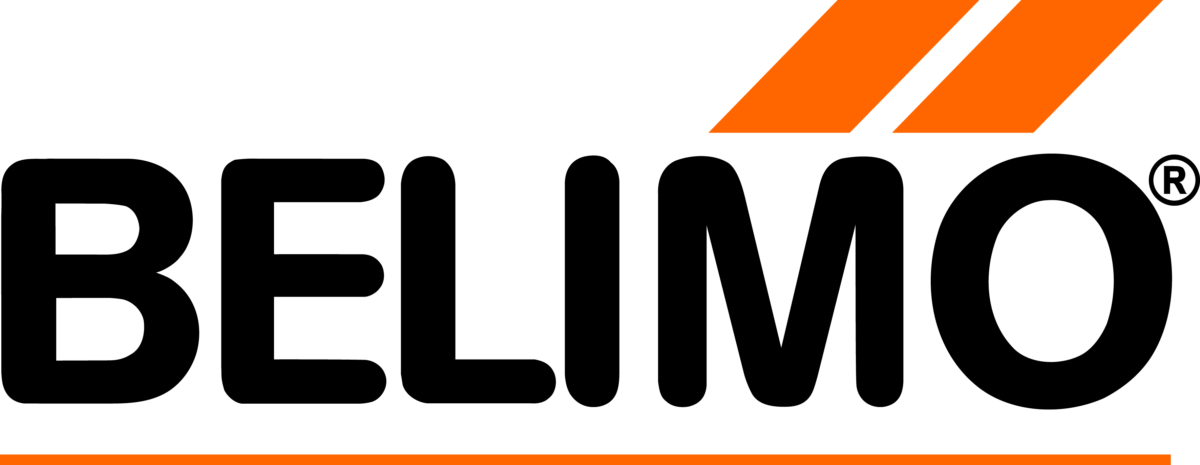