Author: Frank Trompke
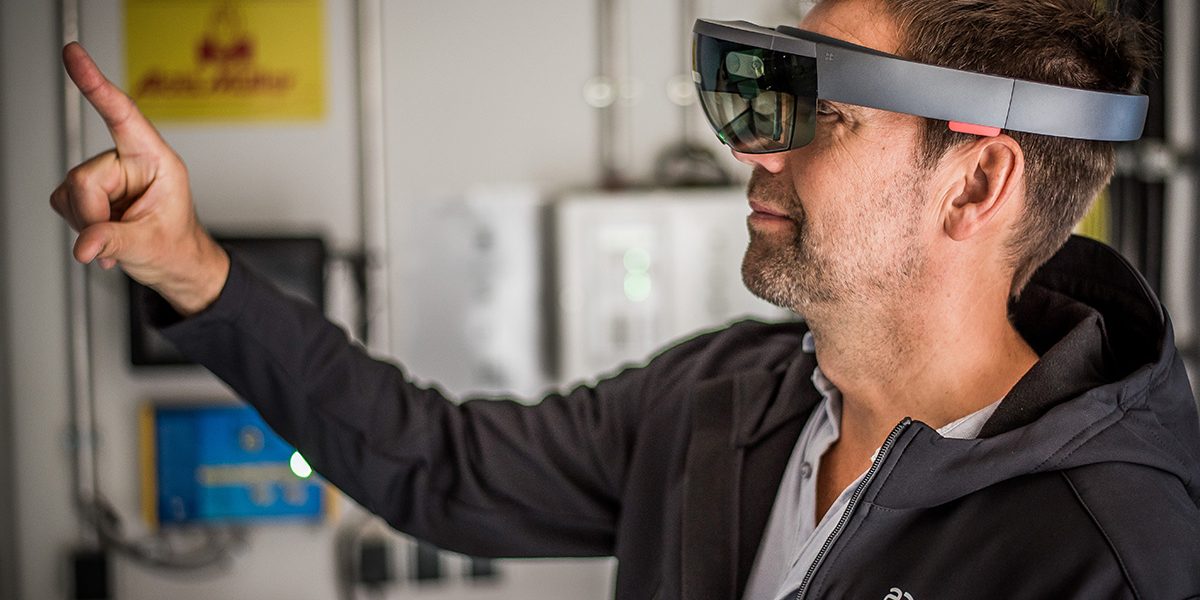
How industrial augmented reality is revolutionizing service and maintenance
If you want to offer excellent service and reliable maintenance, you need the right expertise right on site. We reveal how industrial augmented reality helps to carry out maintenance and repairs more efficiently and reduce costs.
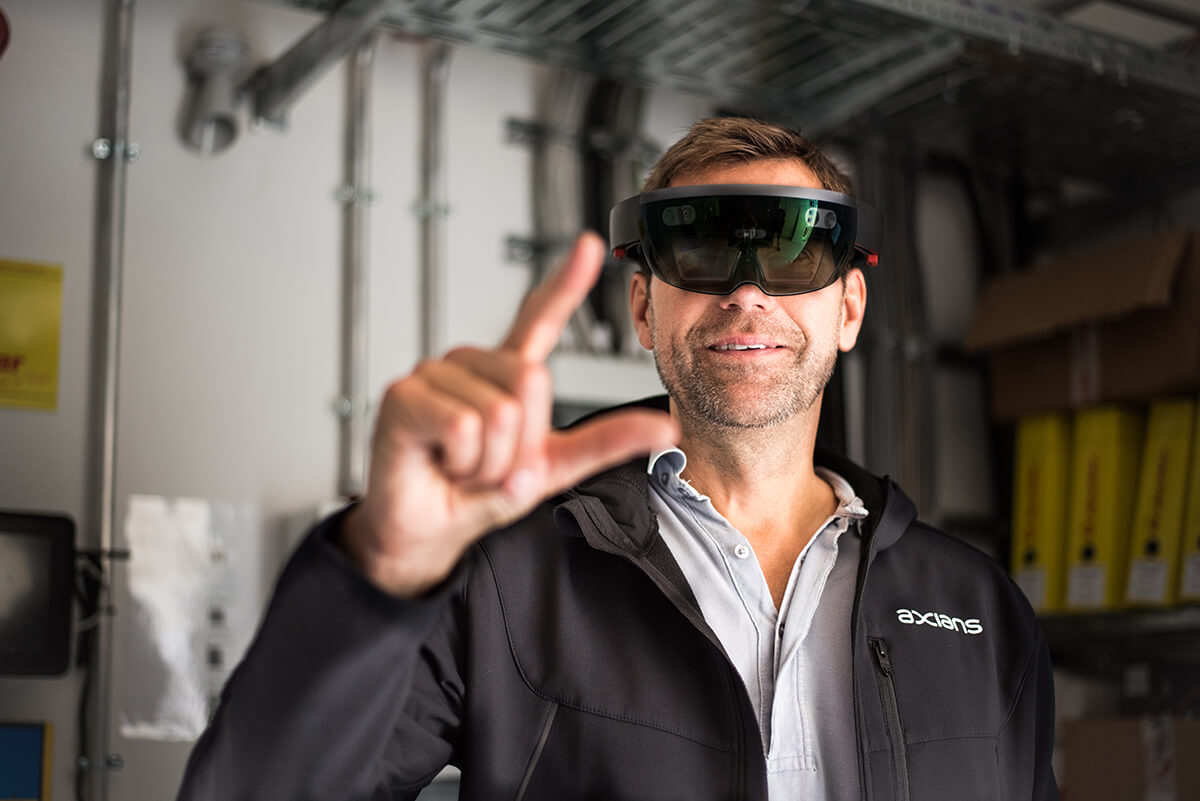
Customer service is a core component, especially for technically oriented companies: If it is “excellent”, it has the potential to increase productivity and customer satisfaction and thus the overall success of a company.
But the The more service availability depends on the company’s own workforce, the greater the impact of the skills shortage. Added to this are the often high training costs and the expectations of the company’s own customers that everything should always run as quickly, transparently and cheaply as possible.
So how can these and other service and maintenance challenges be overcome? Are augmented reality applications a solution that accompany and support service technicians on site?
What is (industrial) augmented reality?
Augmented reality (AR) is a technology that combines digital information – such as images, data and additional contextual information – with the physical world in an “augmented reality”. A camera and a display embedded in a smartphone, tablet or AR glasses are normally used for this purpose. Industrial augmented reality therefore refers to the use of AR technologies in an industrial context. AR can be used in many industrial areas, such as service, maintenance and servicing, to improve processes, increase efficiency and reduce costs.
- Remote support: Service technicians can receive remote support through AR glasses or other devices, with experts giving them instructions and overlaying additional information on the field of vision.
- Maintenance support: AR can display instructions, diagrams and other relevant information directly in the technician’s field of vision to facilitate repair and maintenance work.
- Virtual training: Employees can be trained using AR tools that integrate simulations and interactive learning content directly into their environment.
How augmented reality works in service operations
Imagine a service technician called Michael. Before he gets started with machine maintenance, he briefly puts on his AR glasses. As soon as a tricky problem arises, there is no sign of despair or uncertainty on his face. Why? An expert connected live via AR technology is already connected to Michael to provide visual support from a distance.
Using specific instructions and relevant information, which is immediately projected into Michael’s field of vision, they maneuver together towards a solution. Finally, they check the maintenance data in real time in order to document it and automatically transfer it to the connected CRM system.
This or something similar is already happening in many companies: The fusion of AR technology with field service management systems enables technicians like Michael to access and implement instructions and guidance directly on site and in real time. 3D models and information come to life and problems can be solved effectively through remote guidance. In addition, augmented reality applications allow .
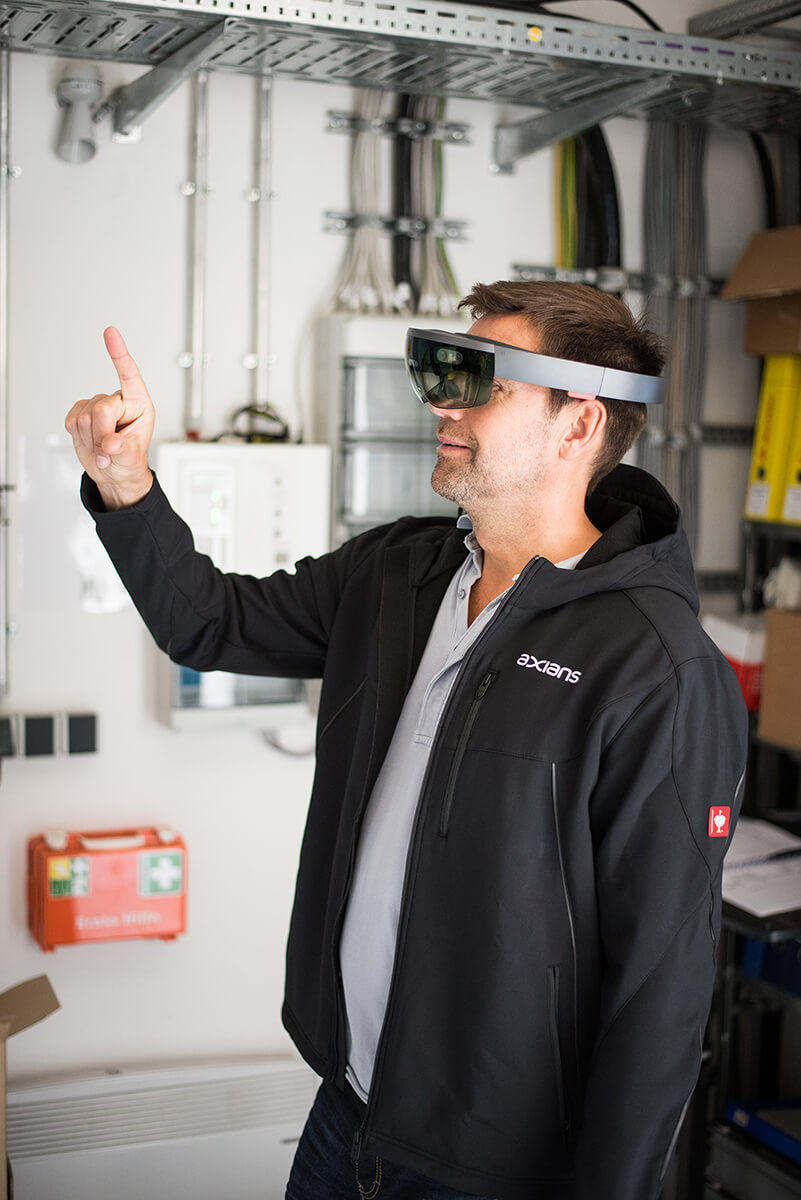
Self-guidance for finding solutions independently
Thanks to industrial augmented reality, technicians can virtually ‘look inside’ machines. This ‘X-ray vision’ allows them to use self-guidance to make components and parts that are difficult to reach or invisible to the naked eye visible. AR also provides visual and therefore easy-to-understand access to work-related data – for example in the form of circuit diagrams, instructions, video guides or other service information, including spare part numbers and material descriptions. The software can also be used to visualize checklists for maintenance or inspections and document progress.
Remote guidance and virtual training
However, augmented reality reveals its true potential when using remote guidance applications, as our technician Michael does. In collaboration with knowledgeable specialists, he can use it to understand everything on site while simultaneously documenting all relevant information and details. In this way, he is guided through all tasks with precise, step-by-step instructions. The result: a reduced error rate, increased first-time fix rate and accelerated service and maintenance activities, as hands-free working and “pick-by-vision” are possible. While the glasses show which utensils are currently required, there is no need to hold an instruction manual in your hands. There is also an efficient transfer of specialist knowledge, as AR is also predestined to disseminate and pass on existing expert knowledge via virtual training courses. This allows employees to familiarize themselves with (new) specialist areas much more quickly, which is a great advantage in times of an acute shortage of skilled workers and digital working methods.
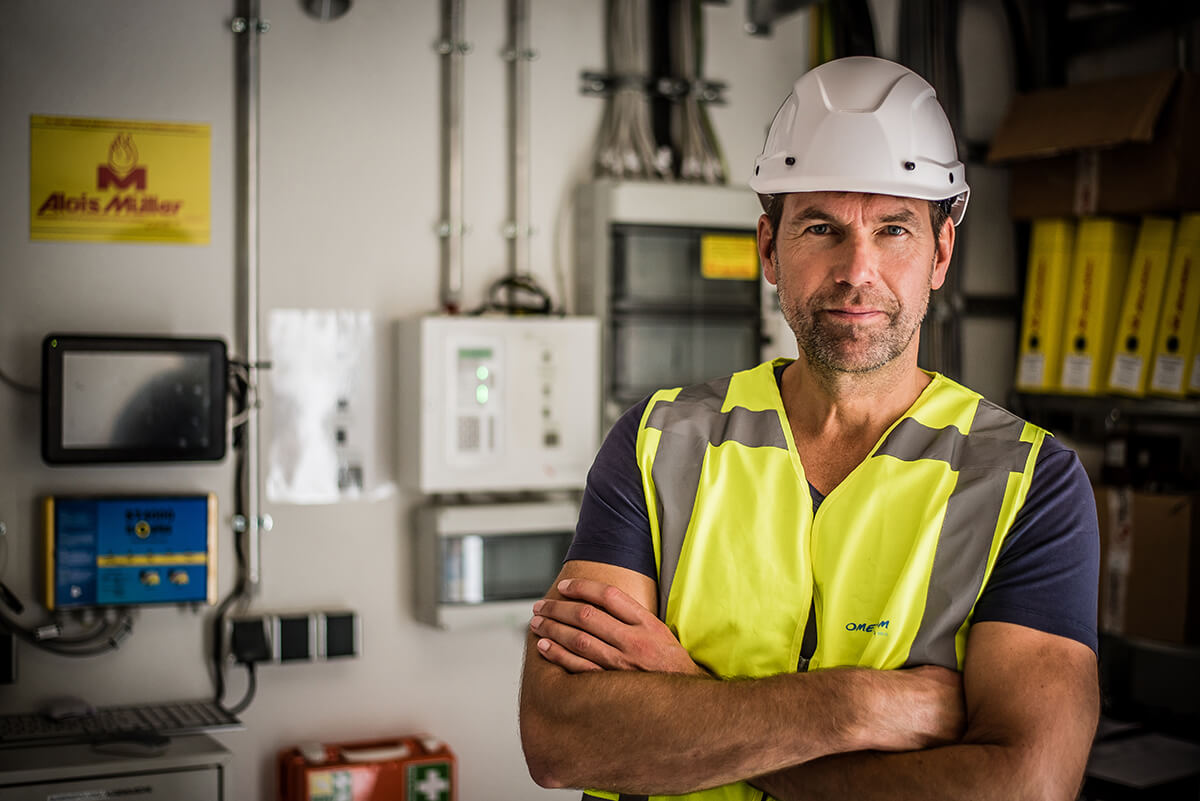
When customers see service processes more clearly
Timely transparency is also a key benefit of AR applications: By clarifying defined milestones and information provided by the CRM system live and in real time, everyone is kept up to date on the current status. And this goes down particularly well with the company’s own customers, who want more insight into the ongoing service processes.
In the event of a fault, the customer also has the option of taking the initiative themselves by scheduling an appointment and receiving support via remote guidance. The employee on site then simply has to put on their AR glasses and follow the instructions given to resolve the problem.
Advantages of augmented reality at a glance:
In times of a shortage of skilled workers, AR applications such as the NEO AR Worker support service and maintenance and thus the company’s own technicians and subcontractors on site. This reduces the number of second trips and improves productivity.
An AR-supported inspection or walk-through provides the technician with the exact sequence of the individual work steps, which reduces the risk of errors and accidents and at the same time improves occupational safety.
Instructions displayed via AR specify the sequence of the individual work steps and simultaneously provide feedback on their correct execution.
As the service employee is shown exactly what they have to do, they can complete their tasks more quickly. There are also fewer second trips, which improves the first-time-fix rate and therefore saves costs.
Customers appreciate speedy maintenance, repairs and a reduced number of follow-up visits. The resulting shorter downtimes and reduced expenses increase customer satisfaction in the long term.
Faster and more effective maintenance or repair of production systems leads to reduced downtimes and thus increases the availability of the systems.
Digital assistance systems have the potential to alleviate or compensate for skills shortages. They offer support for new or less well-trained employees and subcontractors who may not yet be familiar with the machines and systems.
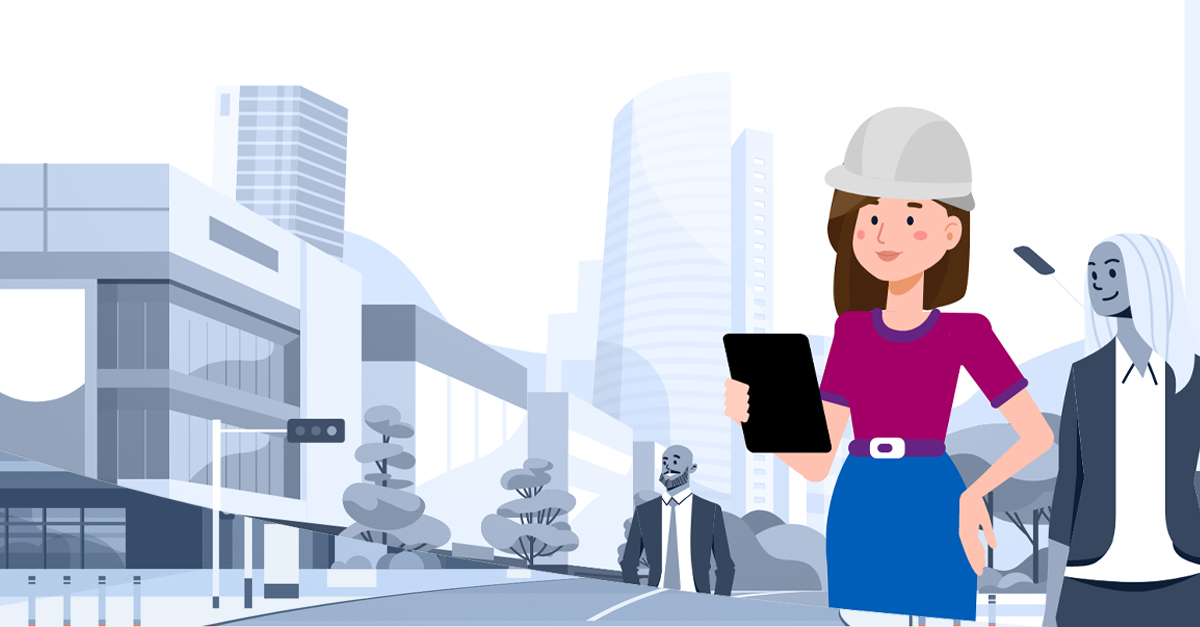
Digitization of your technical customer service
Use industrial augmented reality, offer excellent service
Although it may still sound like science fiction to some, industrial augmented reality has long since made the leap into service and maintenance practice and has found its rightful place in many companies. You can use it to increase productivity and first-time fix rates, save time and costs and increase customer satisfaction. However, as with any other technology, there are challenges with AR remote support that companies should be aware of before deciding to use it. Universal network coverage is a fundamental prerequisite and, of course, a technical platform that provides and collects the required data is also needed in the background. Then nothing stands in the way of “augmented reality”.