Maintenance and repair with the NEO Mobile Suite and NEO Schedule creates stringency and transparency in service. With seamless integration into all upstream and downstream processes along the value chain. With simple scheduling of service teams on site. With a full overview and progress control of all activities.
Customer benefits
Customer
Alois Müller GmbH
Branch
Energy systems | Building technology
Contact
Selina Wagner
Project Manager Axians NEO Suite
+49 621 72926173
Contact us
Mobile plant service as an ERP-integrated process at Alois Müller GmbH
“Energy in focus” is the guiding principle of Alois Müller GmbH. With this in mind, over the past 50 years the company has specialized primarily in the construction of complex systems for heating, cooling, technical gases and electricity for industrial and medium-sized companies. All with the aim of optimizing energy costs, conserving valuable resources and complying with all environmental regulations.
“Service in focus” was the next claim. As part of the S/4 HANA transformation and as a company-wide integrated field service management solution. Or in short: with the NEO Suite.
From SAP to ASAP: Field Service Management via NEO Suite
Alois Müller also knows that the best system is nothing without the right maintenance. Qualified technicians therefore continuously ensure optimum settings and the interaction of the individual components. Before the project started, however, these processes were carried out manually via many interfaces and with media disruptions. In other words, the databases in the entire value chain were Excel, paper, Outlook and craftsman software. The introduction of S/4HANA formed the basis for these increased requirements at Alois Müller. The standard processes of the SAP modules (SD, CS, PM, CO, MM, FI) were used for this, particularly in the service area.
The company was looking for a field service management solution for the consistent and uniform digitalization of service processes. A mobile application should serve as a communicator for scheduling, provide all customer and deployment-relevant data and enable precise, on-time feedback of activities. Customers should also be able to view and confirm the data recorded in the work report. Digital deployment planning should make it easier for dispatchers to schedule orders to the right technicians at the right times for the customer.
The Axians NEO Mobile Suite, which 95 technicians have been using since July 2021, is now used for mobile order processing with all features, data and tools – whether on the road or on site.
The NEO Schedule scheduling solution was introduced in October 2022. Since then, four dispatchers have been scheduling orders and assignments at Alois Müller.
Harmonized processes and freedom offered
With the introduction of the NEO Suite, both employees and customers of Alois Müller experienced a significant improvement in services, coupled with considerably more transparency for all parties involved – whether clients, executing technicians or planners.
Standardized, harmonized processes now not only ensure more efficient work. Centralized control and scheduling of service assignments also saves time and money. Interests and work processes are kept synchronized in the digitalized system. And that also increases productivity.
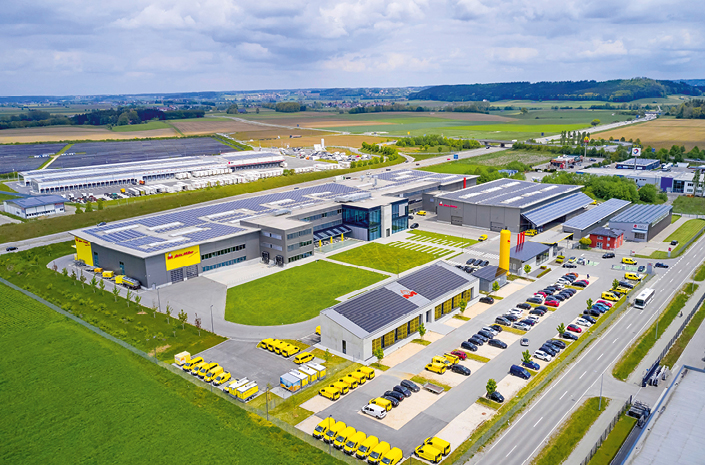
All areas of the company communicate on one level and therefore interact smoothly. The result is a seamless workflow. Whether stationary or mobile, everyone involved in the project is always up to date. And no information is lost along the way. The Alois Müller Service Center is thus able to meet the most diverse requirements of its customers promptly and competently. Even highly complex processes are integrated into the service cycle without compromising on time or quality.
Mobile First Class: NEO with RFID tag
One of the technical specials for Alois Müller was the integration of RFID tags for contactless reading and recognition of the technical objects. RFID is a proven method for identifying objects via radio. By using this technology and integrating it into the solution concept, Alois Müller can now offer additional services.
RFID is used, for example, to check fire dampers. Specifically: A technician walks through the hall and scans RFID tags at a height using the NEO Mobile app. The measuring point is automatically recognized and a measurement document is written. The customer then also has recorded proof that the service technician was actually at the respective system. Another advantage is that the correct object in the list is recognized when the measuring point is detected and the associated checklist processing is started.
Conclusion and outlook: Plus points for mobile service
To expand the scope of services, Alois Müller is currently considering automatic deployment planning with the NEO Optimizer. The migration to the current mobile solution NEO Mobile is also planned.
"We were looking for a standardized solution to map our service processes, while at the same time using individual process functions. The features of the NEO Suite from Axians provided us with the best mix for this: standardized processes paired with functions individually tailored to our requirements. As a result, this is a key factor in our ability to outperform our competitors. After all, no other cloud solution in the service sector could offer us the flexibility that our teams now use on a daily basis with the NEO Suite."
Key user SAP and Head of Controlling, Müller Service GmbH
Alois Müller GmbH. Focus on energy. Mobile service under control.
From a family business founded in 1973 to a medium-sized company, the Alois Müller Group now employs over 800 people at 14 branches. 90 percent of them work in operations. The central “Green Factory” in Ungerhausen, Swabia, is home to the comprehensive production facility for mobile energy centers and energy module systems. Alois Müller generally focuses on a sustainable philosophy. For heating,
Ventilation, sanitary, refrigeration or electrical engineering as well as energy contracting orCO2-neutraland energy self-sufficient production.
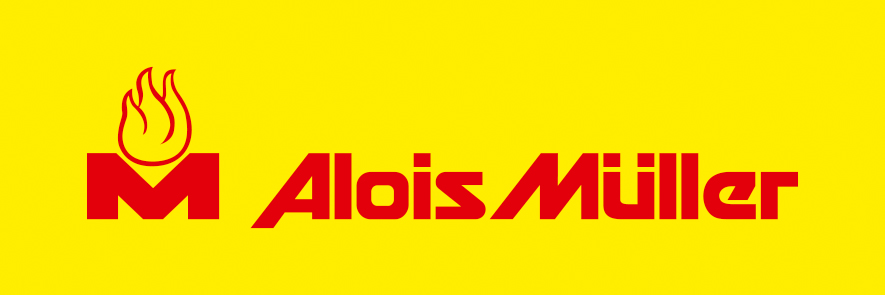