In maintenance (PM), the NEO Suite is used to record and historicize maintenance and repairs to production facilities. In addition to providing a transparent overview of all processes, the mobile app allows the team to process tickets digitally and maintain comprehensive documentation. In customer service (CS), NEO Mobile is used to manage services on objects on site. This includes repairs and rework on completed buildings. The solution offers the integration of SAP processes and end-to-end digital processing of all orders.
From the saw to the service: NEO. The suite for the whole when it comes to sustainable house concepts.
SchwörerHaus KG is one of Europe’s leading companies in the production and construction of prefabricated houses and components for residential and commercial projects. The brand is known above all for its sustainable product philosophy. In keeping with this philosophy, Schwörer uses Axians NEO software for two key success factors: Plant Maintenance (PM project) and Customer Service (CS project).
SchwörerHaus had a clear blueprint for the required solution: a modern and future-proof software application. Specifically: a product based on standard SAP processes that mobilizes, digitalizes and optimizes both maintenance processes in the plants and services for customers. And on a completely new foundation. The existing application was already over 20 years old, based on DOS-like interfaces and devices such as Palms and Windows CE. This architecture therefore proved to be incompatible with new operating systems – and also entailed considerable risks when switching to SAP S/4HANA. Maintenance and repairs were also not systematically documented anywhere. The “knowledge repository” was therefore largely in the heads of long-standing employees.
Two construction sites. One master plan. NEO Suite: the innovative service management for SAP users.
Planning began with workshops with Axians and SchwörerHaus employees to analyze all the requirements of the relevant departments in detail – and then to develop a suitable concept for SAP PM and CS in all respects and subsequently the use and features of the NEO app. The start of the overall project then took place in the area of maintenance (PM) – with productive use of the solution in the shortest possible time. The first requirement here was to ensure system stability and compatibility with the planned SAP S/4HANA conversion. As only reactive processes were currently relevant, it was possible to start with an order and notification type within a very short time. In addition, the entire mobile application had to be simple and intuitive to use in order to ensure acceptance by the maintenance teams. Each production system was also to receive a detailed history of repairs and problems. Not to forget: full digital transparency. In other words, the creation of central documentation for all maintenance and servicing work carried out – including damage codes and documentation with images, which are stored via document info records.
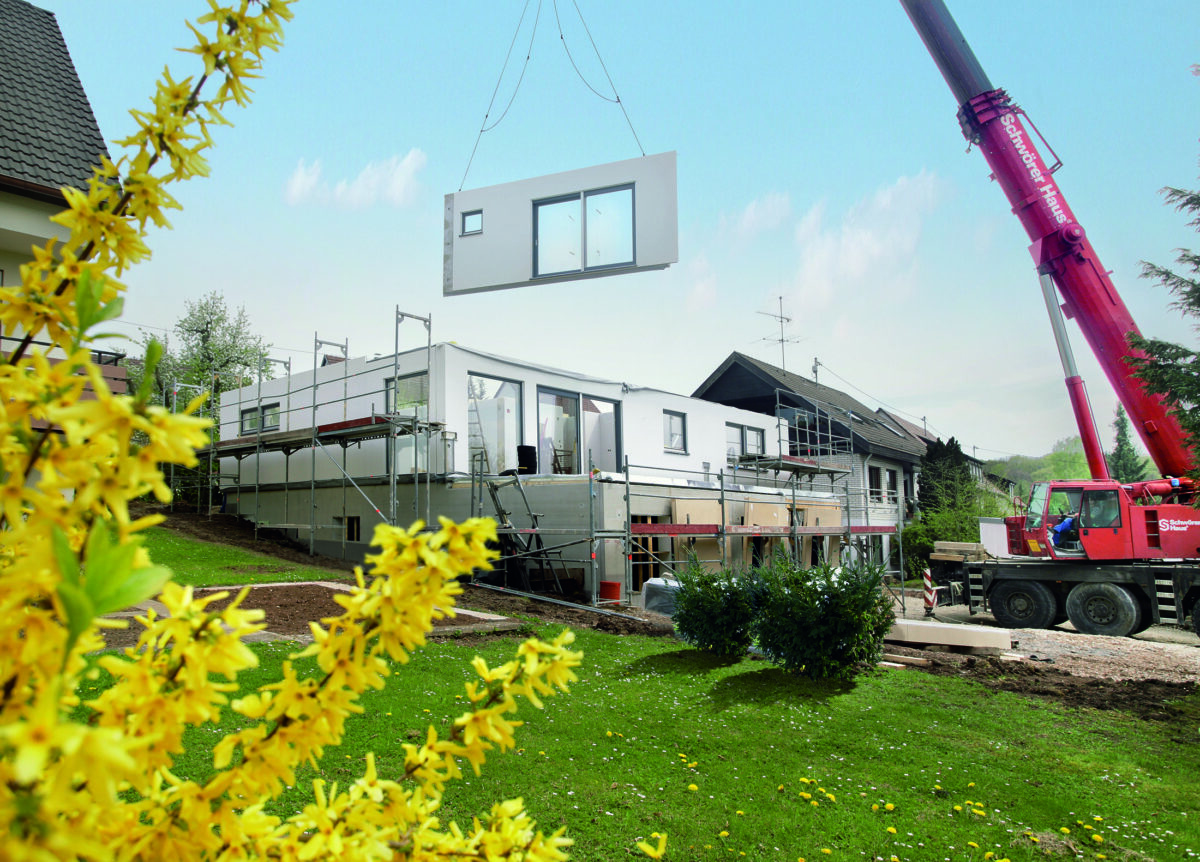
Customer Service by NEO. Mobile First. Right up to roof-first.
For the SchwörerHaus customer service (CS project), the features of the NEO app were further developed and modified on the basis of the PM solution. At the heart of this is the development of a mobile application for processing service orders for buildings on site. This includes the integration of functions such as the recording of material feedback, the connection of existing systems such as external location management and a central overview of all notifications relating to an object. All in all, detailed adjustments were required in order to seamlessly integrate all material flows into the new SAP-based solution. The tickets also involved the integration of the system and SAP. Service notifications for buildings can now be created directly from OTRS tickets to avoid duplicate data entry.
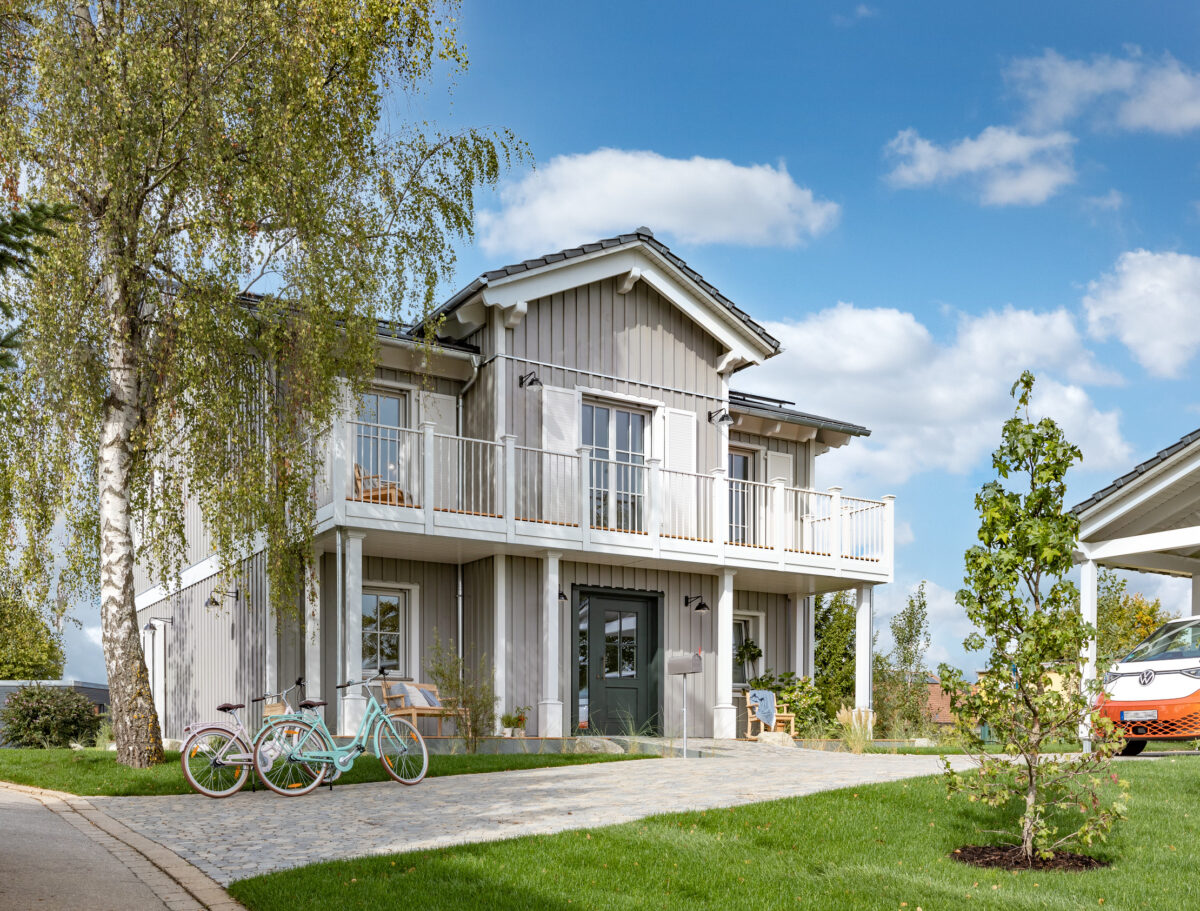
Fully elegant. And quite slim.
The main benefits of the NEO application for Schwörer customer service employees include, in particular, the efficient booking and provision of materials for orders on site. In addition, there are customer-specific adaptations such as the mapping of individual customer requirements – for example, for rework on completed construction projects. And most importantly: keeping everything lean! The entire mobile application was therefore designed in such a way that even employees with little IT affinity can use it to its full extent without any problems.
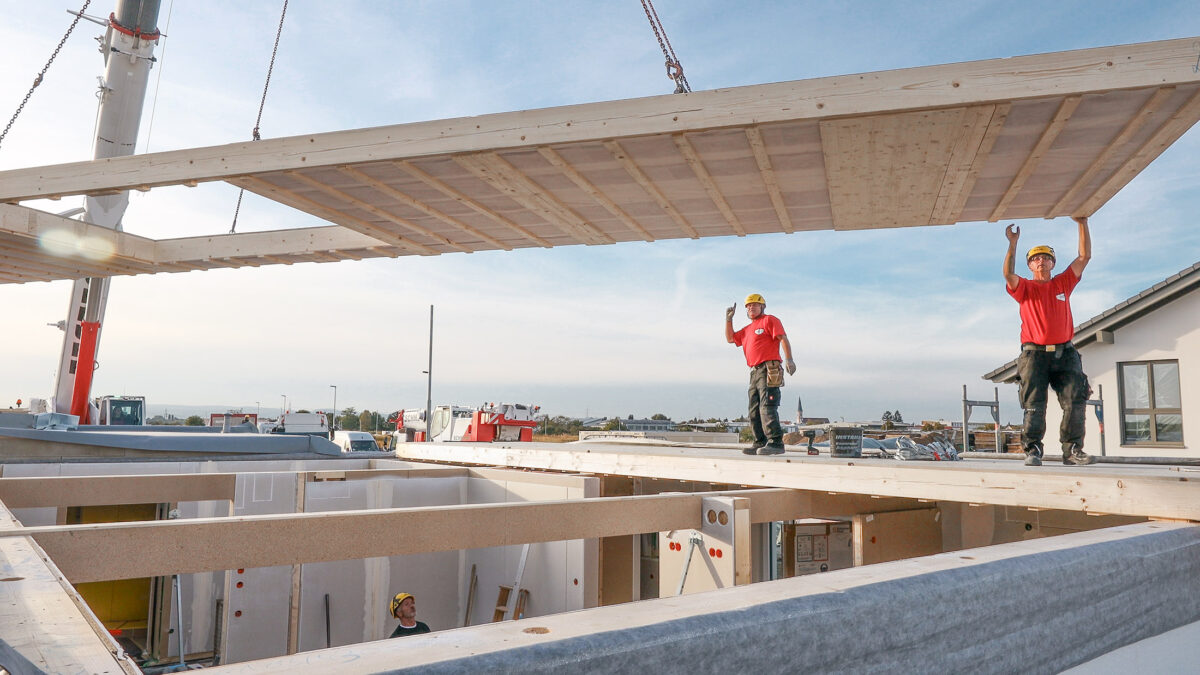
The individual cut is on the agenda.
Solid statics and a suitable floor plan. Axians implemented individual adaptations in the NEO app in line with the needs-based residential construction. In other words, everything to meet the specific requirements of SchwörerHaus. This included setting up catalogs and orders to systematically map all maintenance processes as well as integrating the NEO Mobile Suite for mobile order processing. When developing the dashboard for the office staff, it was particularly important to ensure clear management of orders and notifications. In addition, a start-stop function for time recording and adapted features for the self-scheduling of employees in the maintenance app were integrated. And for the automated transfer of ticket data to the SAP system, mobile customer service now uses an interface between OTRS and SAP via the SAP BTP (Business Technology Platform). In customer service (CS) at SchwörerHaus, around 25 technicians currently use the NEO solution for around 200 assignments per week. In maintenance (PM), there are currently around 10 technicians carrying out maintenance and repairs on production systems or machines – in prefabricated house production and in the timber sawmill. In the PM area, the technicians can also independently select jobs from a pool. Team leaders also have the option of assigning specific jobs.
Fit for Profit: NEO at Work.
Investments must be worthwhile. And the advantages for SchwörerHaus in this NEO project are straight to the point:
through a solution that is always up to date and compatible with the S/4HANA environment
with histories and documentation on all production systems and service orders
including automatic transfer of all relevant data from the ticket system (OTRS) to SAP
via a dashboard with prompt information from all relevant sources
with users through intuitive, smart operation
using features that intelligently optimize work and processes
thanks to the seamless recording and traceability of all service and maintenance measures
The teams at SchwörerHaus are currently working very successfully with the intensive use of Axians NEO’s PM and CS applications. An operational expansion of the PM features in the app is already being planned.
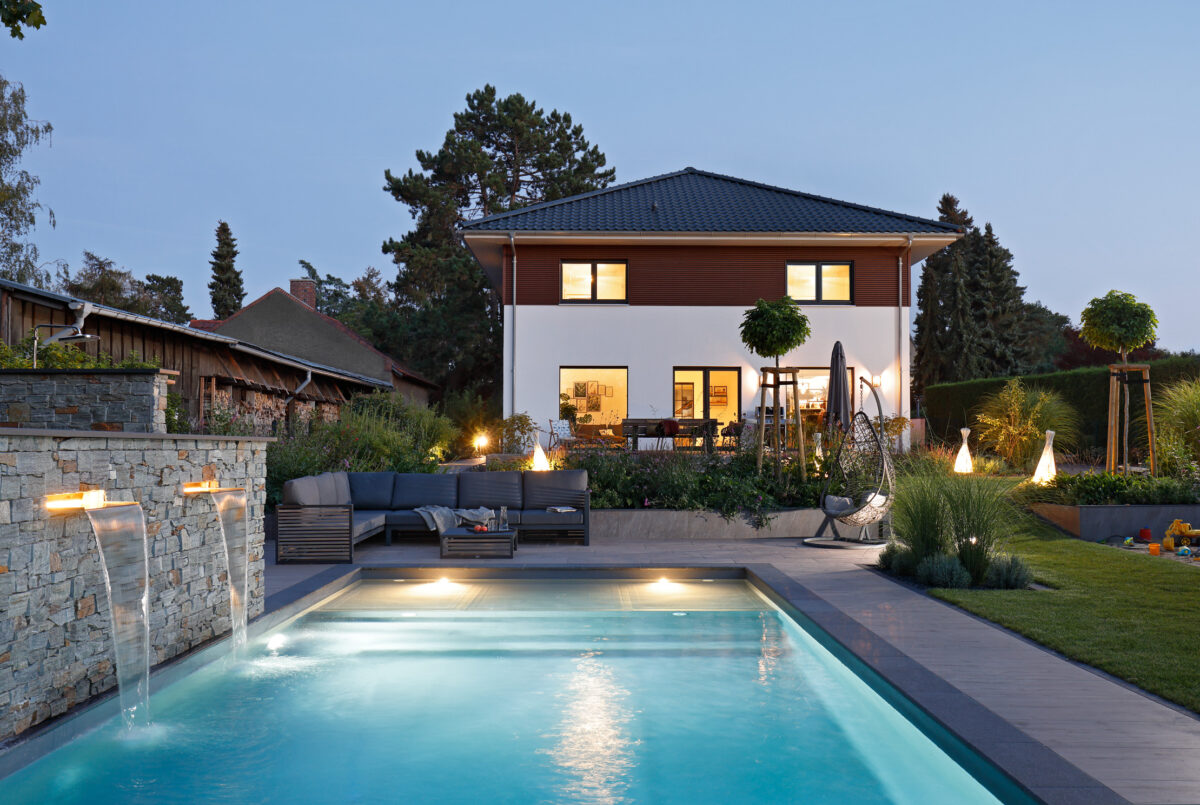
We build all our solutions on three foundations: solidity, innovation and sustainability. The first steps for our mobile maintenance project were therefore already taken in 2019. I was particularly impressed by Axians' presentation. The decision to rely entirely on the NEO app for the implementation was then made not least due to the comprehensive expertise in the area of SAP PM. The general understanding of our internal processes was just as important. In short, trust formed the basis for tailor-made results. As a result, the chemistry was right from the start. Mr. Helmer always found creative ways to find a solution. Not only did he understand our point of view very well - he was also able to communicate this to the developers. Training the fitters, for example, takes less than half an hour. That alone shows how easy and effective the app is to use. This is precisely where the art lies: anyone who sees the NEO applications may not think that it was a challenge to get everything exactly right. But that's what makes this solution so good!
Head of IT | SchwörerHaus KG
Schwörer: Swabian innovation by nature.
SchwörerHaus KG is one of the industry leaders in prefabricated construction. For over 75 years, innovative building concepts and a sustainable philosophy have shaped the values of the family-run company from Hohenstein-Oberstetten in the Swabian Alb. Today, over 1,800 employees work here at seven locations across Germany. The company serves both private customers with individual house construction and business customers – for example in the area of modular construction concepts. And it does so throughout Europe, including in Switzerland, Austria, Italy, France, the Benelux countries and the UK. The range includes single and multi-family houses in timber frame construction, innovative tiny houses, prefabricated parts for basements, garages and other construction projects, modular components for residential construction or hybrid concepts, e.g. for hotels, care homes and social housing. Schwörer consistently focuses on sustainable resource management for its products and production and also operates two company-owned biomass power plants. SchwörerHaus is one of the pioneering climate protection companies in Germany. This was also recognized by the German Sustainability Award 2025.
